-
Spray Drying Machine
-
Vacuum Drying Machine
-
Fluid Bed Dryer Machine
-
Food Production Machines
-
Powder Granulator Machine
-
Air Stream Dryer
-
Hot Air Dryer Machine
-
Dryer Oven Machine
-
Industrial Mixing Machine
-
Grinding Pulverizer Machine
-
Pharma Lift
-
Vibro Screen Machine
-
Multiple Effect Evaporator
-
Hot Air Furnace
-
Heat Exchanger Machine
-
Pulse Jet Bag Filter
-
Waste Heat Recovery Unit
-
Mobile Cip Station
-
KimHello, I got the goods this morning. Very good quality. Thank you so much for doing business with me and you are so patient and clear on explanation.
-
Johnny CisnerosOne of the great positives in working with you and the company you work for is your response back to emails and your professionalism.
Spray Dryer Machine , Embalming Powder Drying Equipment SS304 SS316 FOOD INDUSTRY
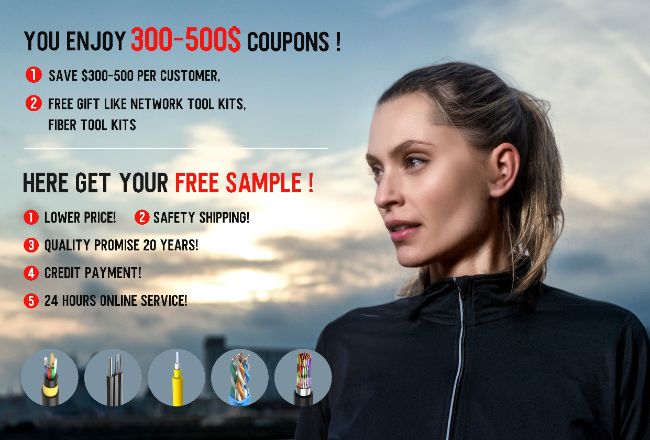
Contact me for free samples and coupons.
WhatsApp:0086 18588475571
Wechat: 0086 18588475571
Skype: sales10@aixton.com
If you have any concern, we provide 24-hour online help.
xMetal Material | SUS316/SUS304/ CARBON STEEL ,ETC | Heating Source | Steam / Electrical / Natural Gas / Diesel / Etc |
---|---|---|---|
Capacity | 10-10000kg Per Hour | Water Evaporation | 5-5000kg Per Hour |
Temp | 120-600'C | Particle | Per Hour |
Highlight | food dryer machine,spray drying equipment,embalming powder spray dryer machine |
LPG Series High speed Centrifugal Embalming Powder Spray Drying Equipment ( high speed centrifugal spray dryer )
Simple Instruction: |
The spray drying is the technology most widely used in the liquid technology shaping and in the drying industry. The drying technology is the most suitable for producing solid powder or particle products from liquid materials, such as: solvent, emulsion, suspension and pumpable paste states, fro this reason, when the particle size and distribution of the final products, residual water contents. Mass density and the particle shape must meet the precise standard, spray drying is one of the most desired technology. |
Working Principle: |
Hot air is distributed downwards with spiral method into the drying tower after filtering and heating. Meanwhile, solution is nebulized millions of single granule and form fog drop. Then the fog drop contact with the hot air and most of the water flash immediately to form the dry product. These powder and granule fall into the air exhaust pipe at the bottom of the drying tower, collected in the material tank. |
Feature: |
|
Preface
Spray drying is the technology most widely used in the liquid technology shaping and in the drying industry. The drying technology is most suitable for producing solid powder or particle products from liquid materials, such as: solution, emulsion, suspension and pump- able paste states. For this reason, when the particle size and distribution of the final products, residual water contents, volume density and the particle shape must meet the precise standard, spray drying is one of the most desired technologies.
After been filtered and heated the air enters into the air distributor on the top of the dryer. The hot air enters into the drying room in the spiral form uniformly. Passing through the high-speed centrifugal sprayer on the top of the tower, the material liquid will rotate and be sprayed into the extremely fine mist liquid beads. Through very short time of contacting the heat air, the materials can be dried into the final products. The final products will be discharged continuously from the bottom of the drying tower and from the cyclones. The waste gas will be discharged from blower.
Feature :
The drying speed is high when the material liquid is atomized, the surface area of the material will increase greatly. In the hot-air flow, 95%-98% of water can be evaporated at a moment. The time of completing the drying is only several seconds. This is especially suitable for drying the heat sensitive materials. Its final products own the good uniformity, flow ability & solubility. And the final products are high in purity and good in quality. The production procedures are simple and the operation and control are easy. The liquid with moisture contents of 40-60% (for special materials, the contents might be up to 90%.)can be dried into the powder or particle products once a time. After the drying process, there is no need for smashing and sorting, so as to reduce the operation procedures in the production and to enhance the product purity. The product particle diameters, looseness and water contents can be adjusted through changing the operation condition within a certain range.
ed centrifugal sprayer on the top of the tower, the material liquid will rotate and be sprayed into the extremely fine mist liquid beads. Through very short time of contacting the heat air, the materials can be dried into the final products. The final products will be discharged continuously from the bottom of the drying tower and from the cyclones. The waste gas will be discharged from blower.
- YIBU conventional Spray Dryer turns liquid into powder in a highly efficient manner. It is used within fields as diverse as the dairy, food and chemicals industries where it has won renown for its performance. With more than 2,500 spray dryers installed worldwide, YIBU Dryer combines experience and cutting-edge technology into added-value solutions for its customers.
- Designed for the specific product to be dried in compliance with a given industry’s standards and requirements, the conventional Spray Dryer produces a fine powder with particle sizes between 20-300 my. It is primarily applied in the chemical industry, but it has also proved valuable in the production of food and dairy products.
- Atomization of the concentrate takes place via either a Rotary Atomizer or high-pressure nozzles. The drying air enters through the air disperser at a high velocity, ensuring optimal mixing with the atomized concentrate. Evaporation is instantaneous, taking place as the droplets pass through the drying chamber.
- Complete control of moisture content, particle structure, particle size distribution, solubility, and wettability, and retention of natural aromas and flavours.
- Unbeatable performance/cost ratio Energy efficient components, continuous and rapid drying, ease of operation and process automation provide complete control over yield and costs.
Technical Data:
specification LPG 5 25 50 100 150 200-3000 Tep of inlet air less than 350°C Tep of outlet air 80-90 (kg/h)
Evaporated capacity
5 25 50 100 150 200-3000 Transmitted Compressed air By machine (rpm)Rotating speed 25000 22000 21500 18000 18000 15000 (mm)
ia. of atomizing disk
50 120 120 120 150 180-340 Heat source Electricity Electricity +
Electricity+ steam, oil fuel, gas
+ Electricity+ steam + Electricity+ steam, oil fuel, gas Solved by customer (kw)
Powder of electric heater
9 45 60 81 99 (%)
Yield of dry powder (%)
≥95 ≥95 ≥95 ≥95 ≥95 ≥95 Installation Size for reference A(mm) 1000 1290 1730 2500 2800 Decided in accordance with actual condition B(mm) 2100 3410 4245 5300 6000 C(mm) 2300 4260 4645 6000 6700 φ D(mm) 1060 1800 2133 2560 2860 E1(mm) 1050 1200 1640 2100 2180 E2(mm) 1050 1200 1640 2100 2180 F(mm) 750 1000 1250 1750 1970 G(mm) 530 1700 1750 1930 2080 H(mm) 530 1300 1800 2600 3050 I(mm) 530 1550 1600 1780 1960