-
Spray Drying Machine
-
Vacuum Drying Machine
-
Fluid Bed Dryer Machine
-
Food Production Machines
-
Powder Granulator Machine
-
Air Stream Dryer
-
Hot Air Dryer Machine
-
Dryer Oven Machine
-
Industrial Mixing Machine
-
Grinding Pulverizer Machine
-
Pharma Lift
-
Vibro Screen Machine
-
Multiple Effect Evaporator
-
Hot Air Furnace
-
Heat Exchanger Machine
-
Pulse Jet Bag Filter
-
Waste Heat Recovery Unit
-
Mobile Cip Station
-
KimHello, I got the goods this morning. Very good quality. Thank you so much for doing business with me and you are so patient and clear on explanation.
-
Johnny CisnerosOne of the great positives in working with you and the company you work for is your response back to emails and your professionalism.
Spray Drying Powder Granulator Machine , Siemens Motor Dry Granulation Machine
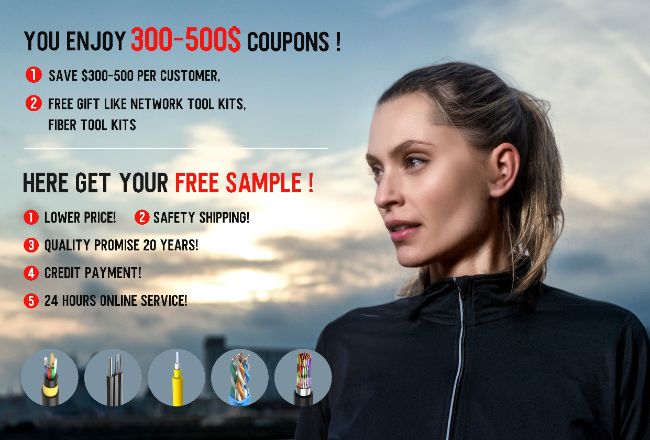
Contact me for free samples and coupons.
WhatsApp:0086 18588475571
Wechat: 0086 18588475571
Skype: sales10@aixton.com
If you have any concern, we provide 24-hour online help.
xMetal Material | SUS316/SUS304/ CARBON STEEL ,ETC | Heating Source | Steam / Electrical / Natural Gas Etc |
---|---|---|---|
Document | FAT/ IQ / OQ / PQ | Motor | ABB/ SIEMENS / |
Temp | Customized | Power Supply | Customized |
Highlight | fluid bed granulator,dry granulation machine |
PGL-B-P Spraying Granulator Machine (Granulating machine)(Granulation machine ) ( Granulating equipment, granulation equipment,Fluid bed spray granulation, Spray agglomeration )
Spray Drying And Granulating Machine Feature:
1. Integrate spraying, drying/fluid granulating in a body and realize granulating in one step.
2. Using the process of spraying, it is particularly suitable for micro auxiliary raw materials and thermal sensitive raw materials. Its power is 1-2 times that FL boiling granulating machine.
3. The final moisture of products can reach 0.1%. It is equipped with powder returning device. The rate of granule forming is more than 95%. 0.2-2 mm of granule
4. The improved inner roller multi-flow atomizer in design can treat the liquid extract with 1.3g/cm3 of gravity.
- the processes of mixing ,granulating and drying ar completed in one step inside the machine.
- It is very safe for operator if explosion take place ,because explosion device is adopted .
- No dead corner . Therefore the loading and unloading are quick, light and clean,meet the requirements of the GMP.
- The filtering system for the Chemical fluidized granulating machine
- The granule from the the Chemical fluidized granulating machine is very soluble .it is better for producing the instant chemical granule
Principle :
The powder granule in vessel (fluid bed) appears in the state of fluidization. It is preheated and mixed with clean and heated air. At the same time the solution of adhesive is sprayed into the container. It makes the particles become granulating that contains adhesive. Being of unceasing dry through hot air, the moisture in the granulating is evaporated. The process is carried out continuously. Finally it forms ideal, uniform and porous granules.
Spray agglomeration moves very small, powder particles in the fluidized bed where they are sprayed with a binder solution or suspension. Liquid bridges are created that form agglomerates from the particles. Spraying continues until the desired size of the agglomerates is reached.
After the residual moisture in the capillaries and on the surface has evaporated, hollow spaces are created in the granulate while the new structure is solidified throughout by the hardened binder. The lack of kinetic energy in the fluidized bed results in very porous structures with plenty of internal capillaries. The usual size range of the agglomerate is from 100 micrometers to 3 millimeters, while the starting material can be micro-fine.
The electronic systems and their safety should comply with the requirements set forth in 21 CFR Part 11 and GMP Annex 11;
The data should be collected at appropriate time intervals and stored in the system in a fixed format that can be printed out/read;
Item | Unit | Model | |||||||
PLG-3 | PLG-5 | PLG-10 | PLG-20 | PLG-30 | PLG-80 | PLG-120 | |||
Liquid extract | Min. | kg/h | 2 | 4 | 5 | 10 | 20 | 60 | 100 |
Max. | kg/h | 4 | 6 | 15 | 30 | 40 | 100 | 140 | |
Fluidization capacity | Min. | kg/batch | 2 | 6 | 10 | 30 | 60 | 100 | 150 |
Max. | kg/batch | 6 | 15 | 30 | 80 | 160 | 250 | 450 | |
Specific gravity of the liquid | kg/L | ≤1.30 | |||||||
Volume of material container | L | 26 | 50 | 220 | 420 | 620 | 980 | 1600 | |
Diameter of container | mm | 400 | 550 | 770 | 1000 | 1200 | 1400 | 1600 | |
Power of suction fan | kw | 3 | 5.5 | 7.5 | 11 | 15 | 18.5 | 30 | |
Power of auxiliary fan | kw | 0.35 | 0.75 | 0.75 | 1.2 | 2.2 | 2.2 | 4 | |
Steam | consumption | kg/h | 40 | 70 | 99 | 210 | 300 | 366 | 465 |
pressure | Mpa | 0.40~0.60 | |||||||
Power of electric heating | kw | 9 | 15 | 21 | 25.5 | 51.5 | 60 | 75 | |
Compressed air | consumption | m3/min | 0.5 | 0.8 | 0.8 | 0.9 | 1.1 | 1.3 | 1.8 |
pressure | Mpa | 0.40~0.60 | |||||||
Operating temperature | °C | automatically regulated from indoor temperature to 160°C | |||||||
Water content of product | % | ≥0.2% | |||||||
Rate of product collection | % | ≥99% | |||||||
Noise level of machine | DB | <77 | |||||||
Dimension of main machine | Φ | mm | 400 | 550 | 770 | 1000 | 1200 | 1400 | 1600 |
H1 | mm | 940 | 1050 | 1070 | 1220 | 1570 | 1590 | 1690 | |
H2 | mm | 1900 | 2360 | 2680 | 3150 | 3630 | 4120 | 5050 | |
H3 | mm | 2050 | 2590 | 3020 | 3600 | 4180 | 4770 | 5800 | |
B | mm | 740 | 890 | 1110 | 1420 | 1620 |