-
Spray Drying Machine
-
Vacuum Drying Machine
-
Fluid Bed Dryer Machine
-
Food Production Machines
-
Powder Granulator Machine
-
Air Stream Dryer
-
Hot Air Dryer Machine
-
Dryer Oven Machine
-
Industrial Mixing Machine
-
Grinding Pulverizer Machine
-
Pharma Lift
-
Vibro Screen Machine
-
Multiple Effect Evaporator
-
Hot Air Furnace
-
Heat Exchanger Machine
-
Pulse Jet Bag Filter
-
Waste Heat Recovery Unit
-
Mobile Cip Station
-
KimHello, I got the goods this morning. Very good quality. Thank you so much for doing business with me and you are so patient and clear on explanation.
-
Johnny CisnerosOne of the great positives in working with you and the company you work for is your response back to emails and your professionalism.
SGS Standard Air Stream Spin Ryonet Flash Dryer Micro Negative Pressure Operation
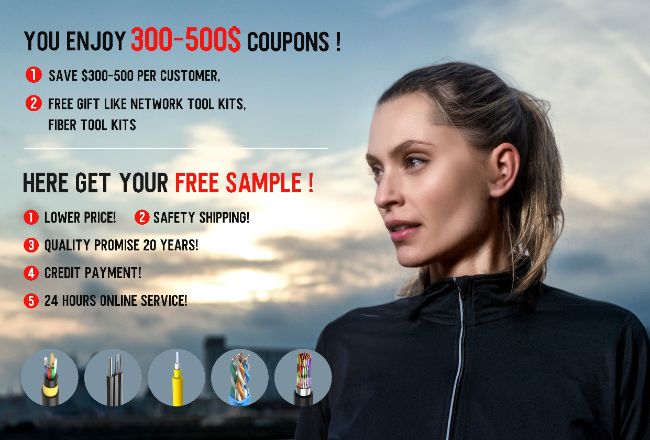
Contact me for free samples and coupons.
WhatsApp:0086 18588475571
Wechat: 0086 18588475571
Skype: sales10@aixton.com
If you have any concern, we provide 24-hour online help.
xMetal Material | SUS316/SUS304/ CARBON STEEL ,ETC | Heating Source | Steam / Electrical / Natural Gas / Diesel / Etc |
---|---|---|---|
Temperature | 100-500℃ | Capacity | 200-8000kg/h |
Water Evaporation | 10-2000kg/h | Power | Customized |
Highlight | hot air dryer,spin flash dryer,sgs standard spin flash dryer |
Flash Drying Machine (Spin Flash dryers ) (Rotating flash Dryer)( Flash cooler )
Preface
Wet material is dispersed into a stream of heated air (or gas) which conveys it through a drying duct. Using the heat from the airstream, the material dries as it is conveyed. Product is separated using cyclones, and/or bag filters. Typically, cyclones are followed by scrubbers or bag filters for final cleaning of the exhaust gases to meet current emission requirements.
Feed system
The feed system consists of a feed vat where a discontinuous flow of product is buffered and fragmented by an agitator prior to continuous drying. A variable speed feed screw (or pump in the case of fluid feed) forwards the product to the drying chamber.
Drying chamber
The rotor at the conical base of the drying chamber fluidizes product particles in a drying-efficient hot air flow pattern in which any wet lumps are rapidly disintegrated. Hot air is supplied by a temperature-controlled air heater and speed-controlled fan, entering the drying chamber at a tangent in order to establish a turbulent, whirling air flow.
Airborne, fine particles pass through a classifier at the top of the drying chamber, while larger particles remain in the air flow for further drying and powdering.
The drying chamber is rigidly designed to withstand pressure shock in the event of explosive combustion of flammable particles. All bearings are effectively protected against dust and heat.
Bag filter
Powder from the drying chamber is collected in bag filter, while the outlet airleaves the system at the top via a suction fan.
Pneumatic coolers are a simple and reliable method of cooling and conveying dried product. In many instances ambient air will achieve the desired cooling duty. Where required, greater cooling capacity and a finer degree of control can be achieved with conditioned air at a controlled humidity and temperature.
Feature :
1. This machine combines the whirl technology with the fluidity, ejection and smashing step technologies.
2. The equipment is compact and small in size, high in production efficiency and continuous in the production. It has realized that " small equipment can perform the large production".
3. The drying capacity for this machine is big but its energy consumption is low. Its heat efficiency is high.
4. The material stay time is very short. The quality of the final products is very good. The machine can be used for drying the heat sensitive materials.
5. For the negative pressure or the micro-negative pressure operation, the machine is good for its tightness and high in the efficiency so as to eliminate the environmental pollution.
6. High drying efficiency providing low energy costs
7. Continuous processing with short processing time
8. Low operator overheads and minimum maintenance costs
9. Controlled residence time enabling high temperature drying
10. Available in cGMP compliant configurations
spec | Barrel diameter(mm) | Main machine dimensions(mm) | Main machine power ( kw ) |
air velocity ( m3/h ) |
Water evaporation capacity ( Kg/h ) |
XSG-2 | 200 | 250×2800 | 5-9 | 300-800 | 10-20 |
XSG-3 | 300 | 400×3300 | 8-15 | 600-1500 | 20-50 |
XSG-4 | 400 | 500×3500 | 10-17.5 | 1250-2500 | 25-70 |
XSG-5 | 500 | 600×4000 | 12-24 | 1500-4000 | 30-100 |
XSG-6 | 600 | 700×4200 | 20-29 | 2500-5000 | 40-200 |
XSG-8 | 800 | 900×4600 | 24-35 | 3000-8000 | 60-600 |
XSG-10 | 1000 | 1100×5000 | 40-62 | 5000-12500 | 100-1000 |
XSG-12 | 1200 | 1300×5200 | 50-89 | 10000-20000 | 150-1300 |
XSG-14 | 1400 | 1500×5400 | 60-105 | 14000-27000 | 200-1600 |
XSG-16 | 1600 | 1700×6000 | 70-135 | 18700-36000 | 250-2000 |
Principle
- YIBU Spin Flash dryers are designed for continuous drying of cohesive and non-cohesive pastes and filter cakes, as well as high-viscosity liquids. The main components in an YIBU Spin Flash plant are a feed system, the patented drying chamber and a bag filter. Widely acclaimed by customers in a variety of industries all over the world, this patented process provides a faster and more energy-efficient alternative to spray drying. With more than 150 YIBU Spin Flash dryer installations world-wide YIBU DRYING combines experience and cutting-edge technology into added-value solutions for our customers. Elevated drying temperatures can be used with many products since the flashing off of surface moisture instantly cools the drying gas without appreciably increasing the product temperature which may damage its quality.
- Wet material is dispersed into a stream of heated air (or gas) which conveys it through a drying duct. Using the heat from the airstream, the material dries as it is conveyed. Product is separated using cyclones, and/or bag filters. Typically, cyclones are followed by scrubbers or bag filters for final cleaning of the exhaust gases to meet current emission requirements.
- The feed system consists of a feed vat where a discontinuous flow of product is buffered and fragmented by an agitator prior to continuous drying. A variable speed feed screw (or pump in the case of fluid feed) forwards the product to the drying chamber.
- The rotor at the conical base of the drying chamber fluidizes product particles in a drying-efficient hot air flow pattern in which any wet lumps are rapidly disintegrated. Hot air is supplied by a temperature-controlled air heater and speed-controlled fan, entering the drying chamber at a tangent in order to establish a turbulent, whirling air flow.
- Airborne, fine particles pass through a classifier at the top of the drying chamber, while larger particles remain in the air flow for further drying and powdering.
The drying chamber is rigidly designed to withstand pressure shock in the event of explosive combustion of flammable particles. All bearings are effectively protected against dust and heat.